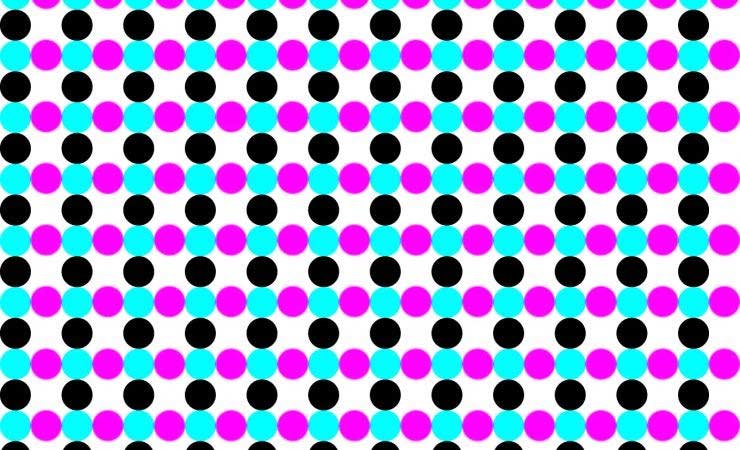
Screen time
Hammilroad says that ‘highly advanced flexo screening technology,’ is giving longer life to flexo
Screening is a vital part of the print production process and printers underestimate it at their peril. Charlie Kortens investigates
Screening is the technique employed in the printing process to simulate shades of grey (tone) or colour and reproduce photographs using combinations of dots from a limited number of coloured inks,’ said Pierre Hammond, commercial director at Hamillroad Software when asked to explain the process in the ‘simplest possible terms
‘It is necessary because printing presses are practically limited to printing solid areas of ink with a fixed number of pigmented process colour inks, normally cyan, magenta, yellow and black (CMYK). Black ink is used to produce a darker result than the often grey-looking colour produced when mixing cyan, magenta and yellow inks, as well as being a lot cheaper. More expensive custom ‘spot colour’ inks are also commonly used to reproduce particular brand colours that are difficult to simulate using just CMYK, or those that don’t print well.
‘Where a larger tonal range is required than can be simulated with just CMYK, Expanded Colour Gamut (ECG), or Expanded Gamut Printing (EGP) techniques may be used.
Here typically seven different inks are used, adding Orange, Green and Violet (OGV) to the existing CMYK set; these additional inks increase the colour gamut of what can be printed accurately.
‘Many types of screening have been developed employing different strategies or techniques for how the dots are shaped, sized and positioned relative to each other which results in different characteristics, each with specific advantages and potential problems, some of which are extremely serious.’
Varieties
Of course, when it comes to screening there are different ways of doing things, depending on a printer’s circumstances. As Robert Bruce, Esko’s product manager for flexo software, explains, ‘When looking at the basics of flexo screening, there are really five key factors to consider. The first is the imaging resolution, which is determined by the spot or pixel size of the imaging device. The resolution determines the number of pixels available for an individual dot, with the most common being 2540 dpi.
‘There is an obvious correlation between imaging resolution and the second key factor, screen ruling. Screen ruling is determining print quality, in that the higher the resolution, the more defined images are, leading to a superior quality final print.
‘The third factor is the dot shape. There are numerous dot shapes available to the flexo printer such as circular, Euclidean, square, elliptical, or even rugby ball shaped. Different dot types can be linked to the imaging device and are sometimes favoured when printing on different substrates, like the age-old film versus paper debate.
‘The type of screen itself is the next key factor. Amplitude Modulation screening, or AM, is a common type of screening used throughout the industry. It enables the use of a multitude of dot shapes which, when printed flexographically, typically appear very smooth to the naked eye. Less common is Frequency Modulated screening – or FM. With
FM screening, the dot size of the screen remains the same, whilst the frequency varies to create different tonal values. While FM screening can be created at a higher line count compared to AM screening, they can have a visible ‘grainy’ appearance once printed. Today, the most common screen type is actually a combination of both AM and FM processes to achieve a desired look. Known as transitional screening, this involves the blending of AM into FM screening in the highlights and shadows, commonly used to make images have a natural fade to zero or to 100%, without the customary ‘hard edge’ associated with flexo printing.
‘Finally, there is surface screening, which as the name suggests adds a surface pattern to the printing dot on the final flexo plate. This process is used to improve ink laydown on film substrates which suffer from reticulation, to improve colour saturation. There are different types of surface screening, which can be applied to both solid and halftone areas. The type of surface screening is dictated by variables such as the ink, substrate, anilox volume and plate type being used, with different screens being required for flexible packaging, labels and corrugated applications.’